Golden Gate Bridge!!!!
- jenniferksampson
- Apr 17, 2017
- 3 min read
Our trip wouldn't be right if we didn't head south to one of the most iconic structures in the world, so here we are, and it lives upto expectation! (the Forth Rail Bridge will also always hold a special place in the list too!)

I'm not sure what I can say about this, except, I could stare at it and the boats passing below it for a long time!
The official opening was by foghorn, 6 a.m. on May 27, 1937, and it's said that that day, nearly 200,000 people walked, tap-danced and roller-skated across it, before it opened to cars the following day. It was the longest suspension bridge in the world.
It's all about the colour:
Apparently the navy and air corps wanted it painted in stripes, but they couldn't agree on colours. It ended up being the well-known red/orange of today because that was the primer colour that was used to protect against corrosion when the steel was sent to San Francisco, and the architect liked it so much! It was also agreed that it would be more visible in fog than a standard grey or black.
It's all about collaboration:
The original design of a cantilever and suspension bridge hybrid by chief engineer Joseph Strauss in 1921 was apparently universally rejected as too ugly. One person even claimed that it resembled “an upside-down rat trap.” This led Strauss to collaborate with rival engineers to produce the graceful suspension bridge design as seen today.
It's all about safety: For its era the Golden Gate Bridge had an impressive construction safety record. In the 1930s, it was generally expected that during steel bridge construction there would be one fatality for every $1 million in cost. During the $35 million Golden Gate Bridge project, 11 construction workers died, which was seen as impressive. This is attributed to the fact that Joseph Strauss made safety a high priority on the project. The construction site was the first in America to require workers to wear hard hats, and he spent a reported $130,000 on an innovative safety net that was suspended under the bridge deck. This net saved the lives of 19 workers who fell from the bridge, and called themselves the “Halfway to Hell Club.” 10 of the 11 deaths actually happened in a single accident on February 17, 1937, when a 5-ton work platform broke away from the bridge and fell through the safety net.
Sadly the Golden Gate Bridge is also famous for another reason, it is one of the top suicide locations in the world. Since opening, more than 1,500 people have jumped from the Bridge (more than 30 bridge jumpers have actually survived). There are 11 crisis counseling telephones on the bridge that connect to trained suicide prevention counselors, and it has just been announced in February 2017, that a notice to proceed was issued for the construction of the suicide deterrent system. This highlights to me the duty we have as engineers to look at a design in terms of all the possible uses and how we can improve to make it safer for all.
It's all about seismic forces:
The bridge is constantly undergoing key retrofit works to enable it to withstand potential earthquakes. Since the large earthquake in 1989, even though the bridge wasn't damaged, there has been a constant list of upgrades.
Two strategies have been employed for seismic retrofit:
1. Strengthening pieces of the bridge to withstand larger forces.
2. Increase flexibility of the structure by fitting seismic isolators. These deform during an earthquake to absorb vibrations and can reduce the impact on the bridge by as much as 2/3 compared to a non-isolated bridge.
The isolator shown here is one on display at the bridge and has been cut in half to show the cross-section of alternating layers of steel and rubber. Sometimes there is a hole in the middle for a lead plug which can further increase energy dissipation. The isolators in the arch section of the bridge are about 1m in diameter!
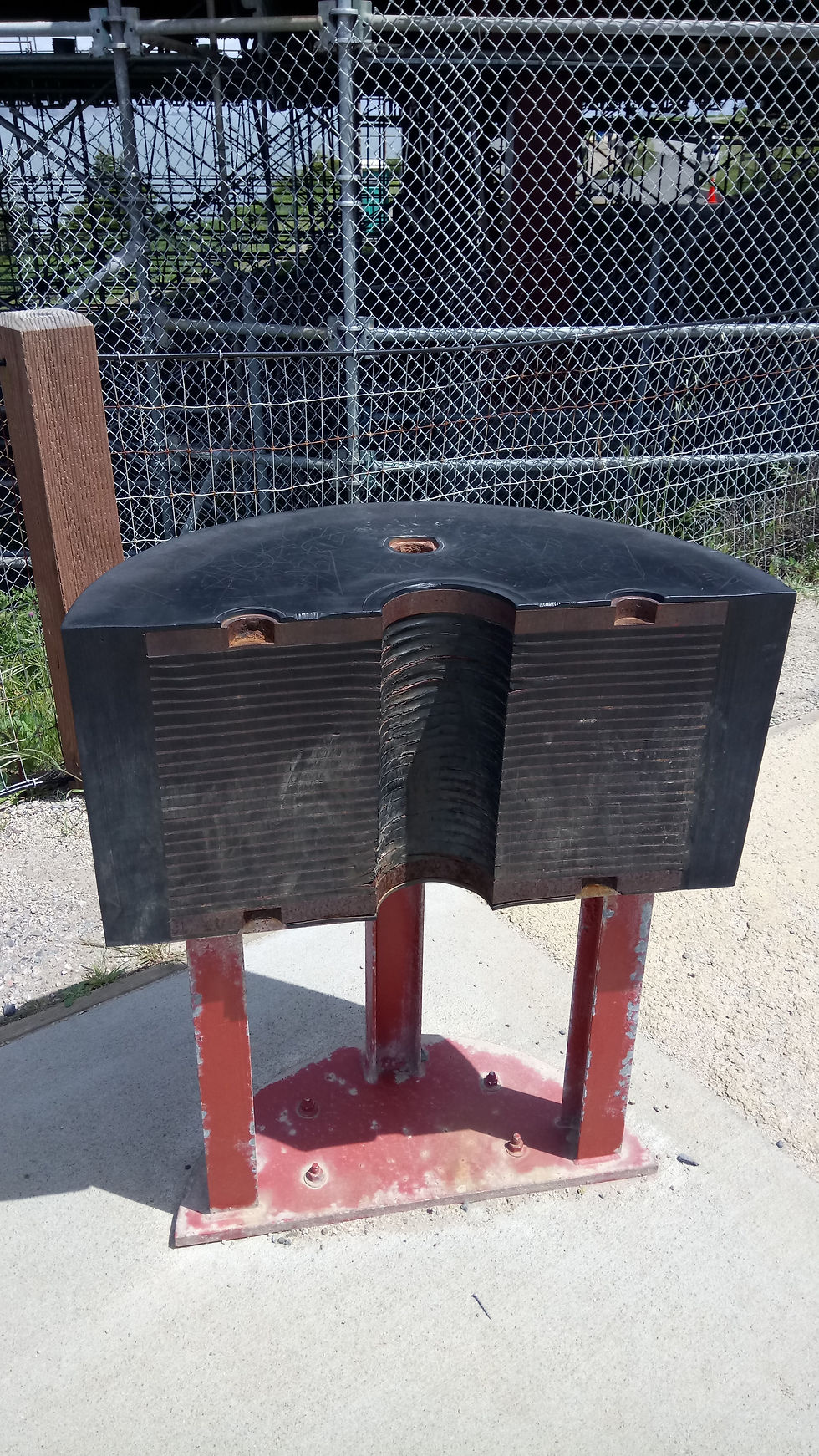
The University of California at Berkeley Civil and Environmental Engineering Department have also made and tested a large replica of the lattice structure, a section of which is on view at the bridge.
The testing machine is 3 stories tall, and can compress with a force of 17.8 Meganewtons, and has meant that far more is now known about the strength of the bridge.
It's all about aerodynamics:
The weight, torsional stiffness and shape of a suspension bridge deck cross-section determines the stability under wind loading. Subtle changes to this cross-section can have a large impact. This was demonstrated in 1940 when the newly constructed Tacoma narrows bridge in Washington State collapsed due to winds of only 40mph. Check it out!! -
https://youtu.be/nFzu6CNtqec
So you'll be pleased to hear, that the project due to be done at the bridge will also include wind loading retrofit works to ensure that the bridge stays safe for use!
Comments